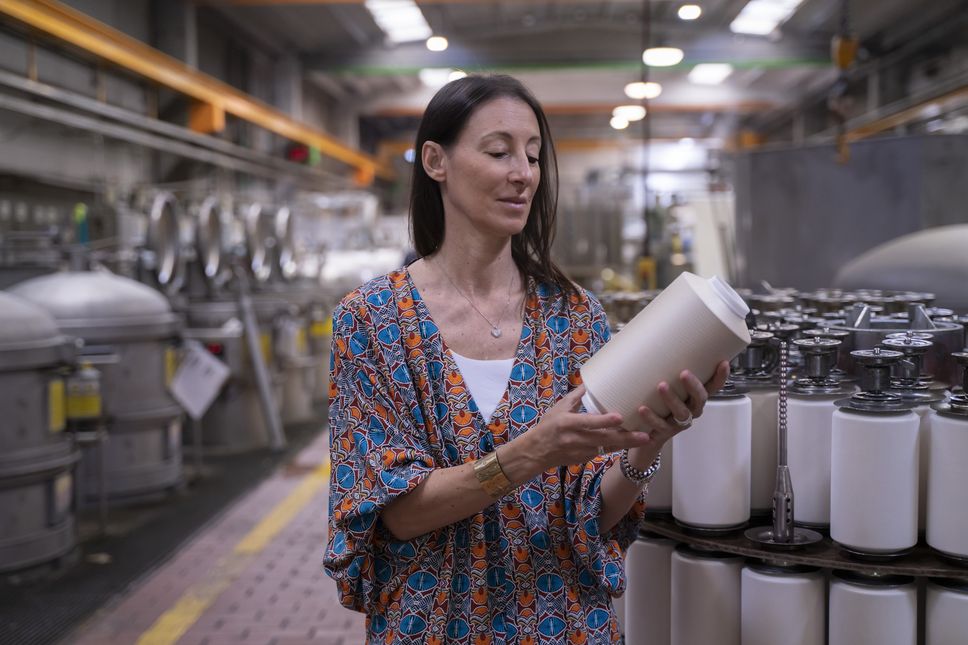
Economia / Como città
Mercoledì 25 Maggio 2022
Dalla sericina agli pneumatici. Como dà valore agli scarti
Il caso di J.And.C.Cosmetici: creme e saponi dalla lavorazione della seta. L’impianto di Holcim: produzione di energia dalla combustione dell’anima delle gomme
Como
Ogni anno tra i 500 e i 600 chili di sericina, proteina tratta dalla purga della seta, diventano, da residui di lavorazione, componente nobile di cosmetici fascia lusso. Sostenibili ed ecologiche, le produzioni della comasca J.And.C. Cosmetici sono un esempio ante litteram di economia circolare. Il recupero dei materiali di scarto, la riduzione degli sprechi, l’utilizzo spesso creativo degli avanzi di produzione sono nella cultura produttiva comasca e non poteva che provenire dal mondo della seta uno dei casi più efficienti di circolarità: già nel ’99 la Tintoria Pecco & Malinverno trovò il modo recuperare la preziosa sericina dal filato puro prima che subisca ogni ulteriore trattamento.
Il processo
Anche se si tratta di un sottoprodotto completamente biodegradabile della lavorazione della seta, per le quantità di sericina che la lavorazione industriale tessile produce si rende necessario smaltirla, con relativi costi per il suo trattamento come rifiuto.
«La sericina è un materiale di scarto ma con caratteristiche uniche, è in grado di rigenerare in modo molto efficace il tessuto cutaneo - spiega Giada Mieli, fondatrice J.And.C. Cosmetici - a fine anni 90 la nostra azienda creò il macchinario per il suo recupero industriale con una riduzione dei costi dello smaltimento, ma soprattutto si aprì la possibilità di un suo utilizzo in cosmetica con una qualità e purezza che la rendono unica al mondo».
L’unicità della lavorazione di questo componente ha permesso al marchio di cosmetici di collocarsi nella fascia alta del mercato. Recente l’accordo con Lario Hotels per gli hotel Vista di Como e di Verona per una linea di cortesia nelle camere dei due 5 stelle lusso che farà conoscere la sericina comasca in tutto il mondo.
Un altro esempio, infinitamente distante, di utilizzo proficuo di un materiale tessile che non avrebbe altro destino oltre alla discarica è il recupero della frazione tessile degli pneumatici delle auto. «Il processo di smaltimento degli pneumatici produce da una parte la frazione di gomma che, trasformata in granulato, viene utilizzata per alcuni tipi di superfici come quella dei campi da tennis - spiega Marco Turri, direttore generale Geocycle, società del gruppo Holcim di Merone - l’altra frazione è l’acciaio che, separato dalla gomma, viene mandato in fonderia. Resta la terza frazione, la parte più interna del pneumatico, una parte tessile che non è possibile rigenerare come materia prima».
Nell’impianto di Ternate in provincia di Varese questo materiale viene lavorato e utilizzato, tramite combustione, per produrre energia.
«L’impianto è in esercizio da metà 2021 e quando sarà a regime ci permetterà di utilizzare circa 10mila tonnellate all’anno di materiale, in sostituzione quasi alla pari di altrettante tonnellate di coke di petrolio - conclude Marco Turri - non possiamo rigenerare quel tessuto, ma possiamo chiudere un ciclo e utilizzarlo per produrre energia invece di un combustibile fossile per il nostro forno, tenuto conto che la produzione di clinker semilavorato, la base per il cemento, è molto energivora».
Ciclo del cemento
Anche il ciclo del cemento realizzato da Holcim è un esempio di economia circolare: le macerie da costruzione e demolizione vengono raccolte, separate, analizzate e lavorate perché siano reinserite nel processo produttivo in sostituzione di nuovi materiali da scavo per poi di nuovo arrivare al cemento come prodotto finito.
Il circolo virtuoso non è in pareggio, ci sono dei limiti tecnici per cui la materia prima può essere sostituita solo parzialmente con materia da recupero che nel processo produttivo di Hocim arriva ad essere diverse decine di migliaia di tonnellate all’anno, che costituiscono qualche punto percentuale sul materiale complessivo.
© RIPRODUZIONE RISERVATA